Nearly four decades ago, Everett Visk started his own badge-making company in his garage in Rancho Cucamonga with an order for less than $20 from a large badge manufacturer in Los Angeles.
Visk, now 82, had left his comfortable job at another large badge manufacturer to strike out on his own.
It was a wise move.
Today, his company, V&V Manufacturing, is one of the most respected manufacturers of specialty custom badges in California, with law enforcement and fire service clients in Orange County and beyond.
One big reason is stellar customer service.
Unlike its competitors – there are three other smaller badge makers like V&V in California, and a couple of huge ones on the East Coast – Visk’s company can turn around badges within 24 hours.
Numerous public safety agencies have relied on V&V, which has been operating out of a 3,000-square-feet warehouse in City of Industry since 1982, to do so when officers and firefighters have been killed on duty, and they need an extra badge to be put in a shadow box.
Sometimes an officer or firefighter is buried in his or her uniform, and another badge is needed. V&V Manufacturing usually can make and deliver those badges in a day.
Steve Visk, 55, who runs V&V with his father, says it’s that commitment to customer service – as well as the quality of V&V’s badges – that sets his niche manufacturer apart from competitors.
“We’ve been approached by police and fire departments whose badges we don’t normally make because their (badge maker) couldn’t do the favor they were asking,” Steve Visk says.
For most badge manufacturers, he adds, the turnaround for a special badge can take several weeks – long after the funeral for the fallen officer or firefighter is held.
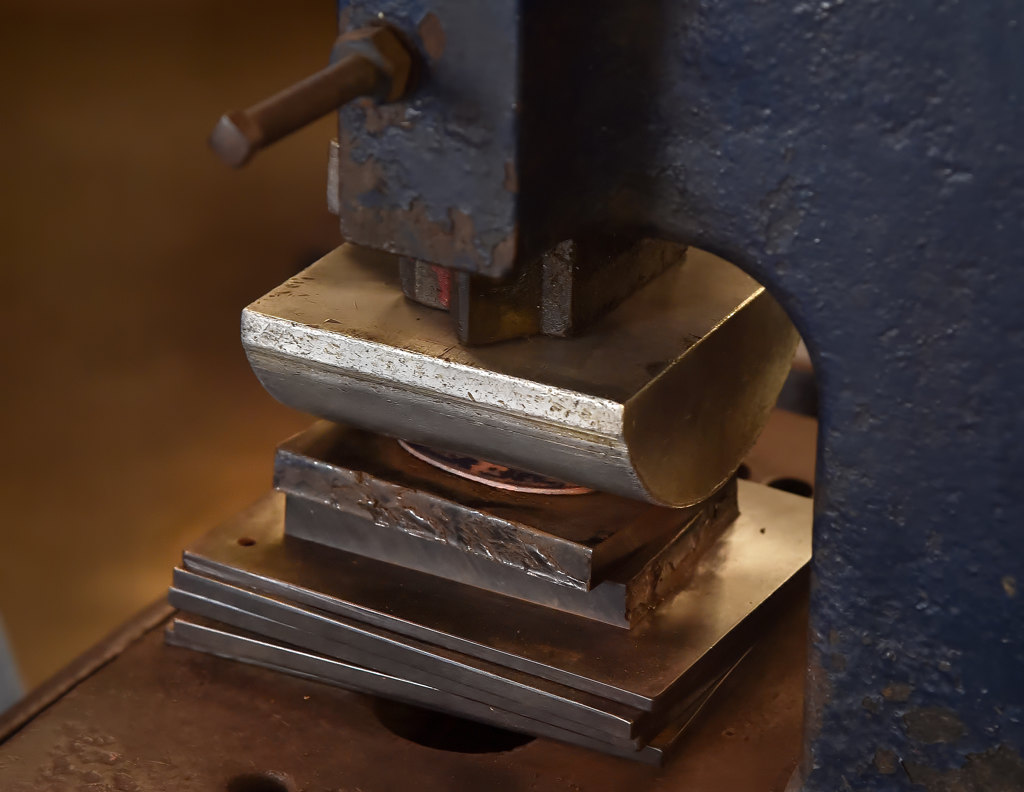
A machine forms a badge into a slightly curved shape at V&V Manufacturing in City of Industry. Photo by Steven Georges/Behind the Badge
“I feel bad for the families whenever I hear a law enforcement officer or firefighter has been killed,” Steve Visk says. “It hurts me. We’ll shut down production to make a badge, and we won’t charge for it. I think that’s really important. We see a lot of cops come in here and talk to a lot of them, and we know their lives and families’ lives.”
Adds Everett Visk: “Police officers perform a public service that not many people appreciate.”
When Long Beach Fire Capt. Dave Rosa was shot to death while responding to an incident at a nursing home on June 25, 2018, the neighboring Seal Beach PD tapped V&V Manufacturing to churn out a special badge for Capt. Rosa to wear when he was laid to rest in uniform. The badge he was wearing when he was killed was given to his family.
The LBFD’s usual badge supplier couldn’t do the job in time for Capt. Rosa’s funeral.
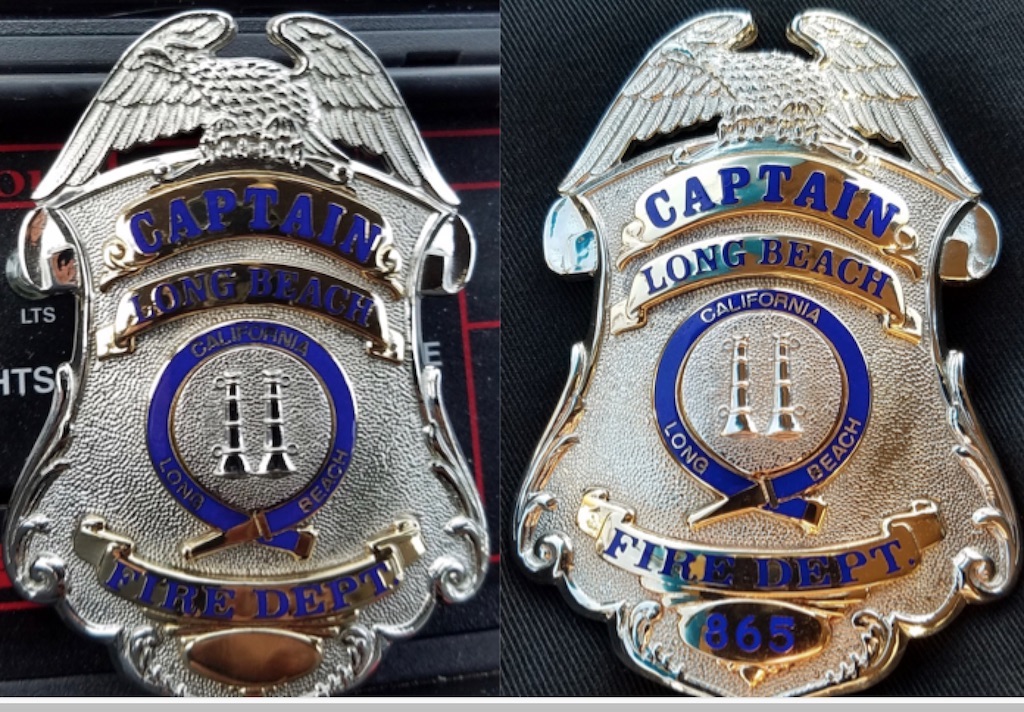
V&V Manufacturing turned around, in less than 24 hours, this badge (right) for slain Long Beach Fire Department Capt. Dave Rosa to wear on his uniform when he was buried. Photo at left is the generic LBFD captain’s badge that V&V had to work on, adding Capt. Rosa’s number. Photo courtesy ofDominic J. Sarabia, Seal Beach PD
The secretary for Long Beach Fire Chief Mike DuRee is friends with the court liaison at the Seal Beach PD, whose badges are made by V&V Manufacturing.
The task of getting the badge made within 24 hours fell on the lap of Dominic J. Sarabia, Senior Community Service Officer, Property & Evidence and Jail Transport, for the Seal Beach PD.
Sarabia used his own car outside of work hours to drive to V&V and give Visk a generic Long Beach FD captain’s badge. Visk was tasked with engraving Capt. Rosa’s number on the badge. It was ready in time for the memorial service the following day. Sarabia made a second trip to V&V to get it.
“They’re really good at assisting (public safety) agencies when they’re in a bind,” Sarabia said of V&V Manufacturing.
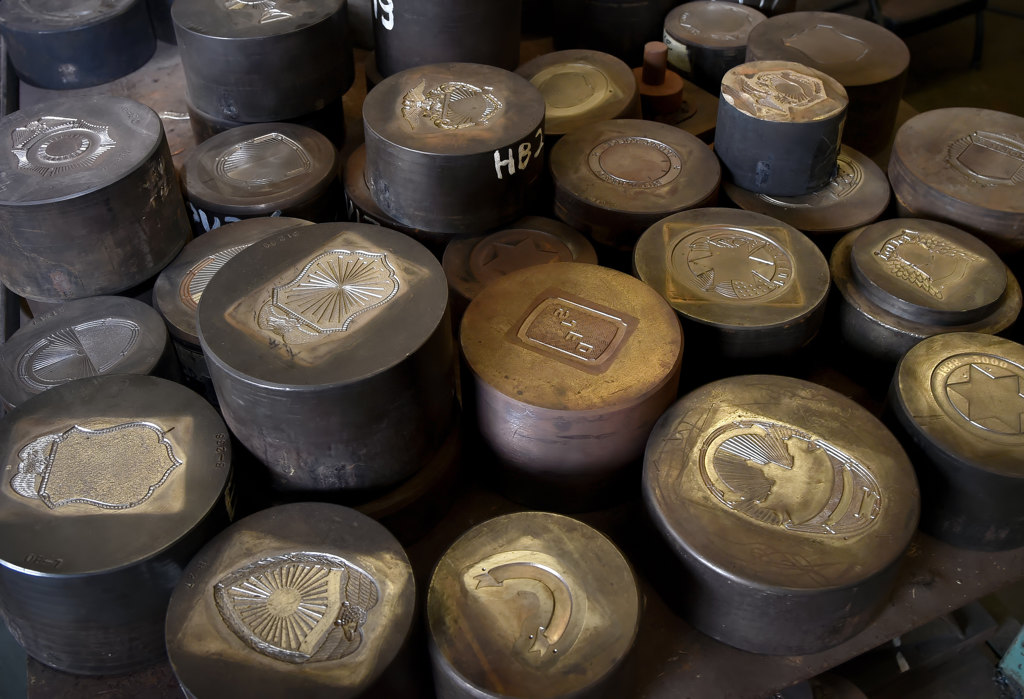
Die stamps of various types of law enforcement badges cost as much as $1,000 a piece.
Photo by Steven Georges/Behind the Badge OC
Following another rush job, Chief Rod Cox of the Cypress PD thanked V&V in a letter for donating services to change the panels on four badges to reflect the badge number of Officer Matthew Ward, who died on Oct. 8, 2017 following an off-duty traffic collision.
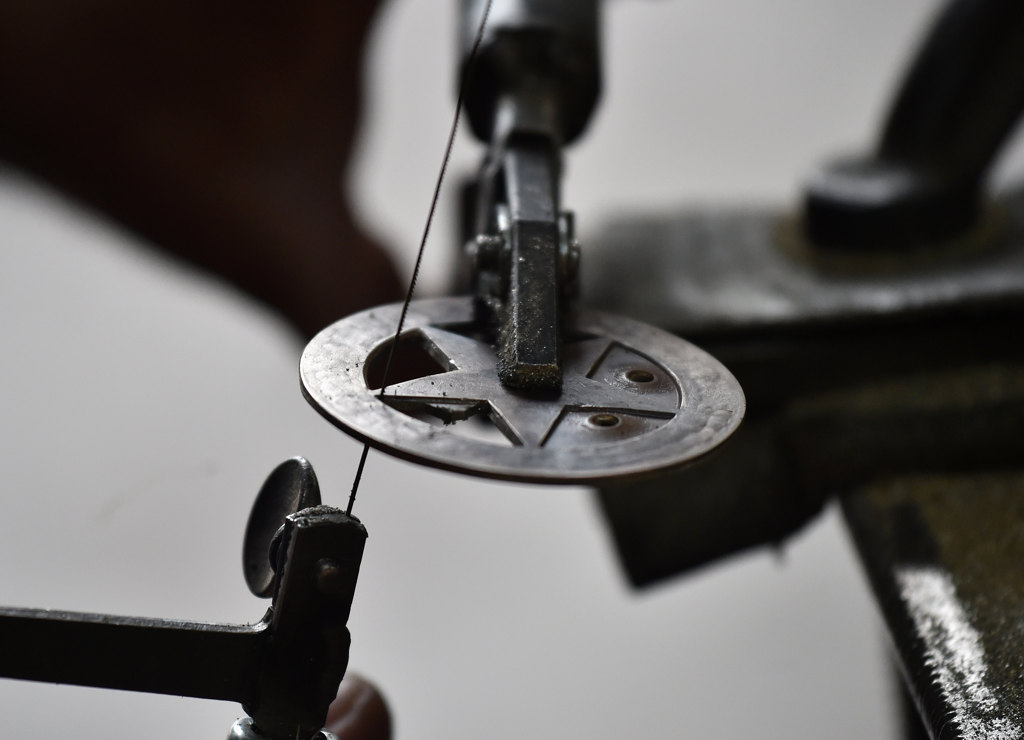
A worker at V&V Manufacturing uses a hand saw on a small-quantity run of badges. Photo by Steven Georges/Behind the Badge OC
“The kindness and generosity of businesses like yours have shone light through the darkness,” Cox wrote.
After an officer for the High Point Police Department in North Carolina was murdered in March 2017, V&V cranked out a badge for his widow at no charge.
“She was overcome with emotion due to your kindness,” Chief of Police Kenneth J. Shultz wrote.
V&V makes badges for 200-plus public safety agencies on a regular basis. The manufacturer can pump out up to 100 badges daily depending on the design.
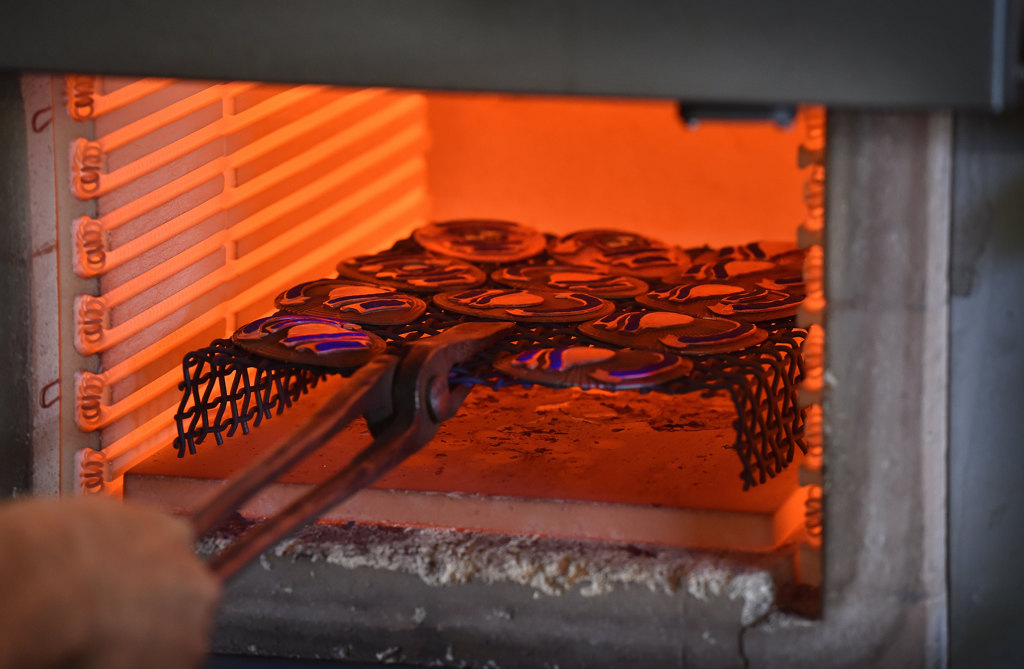
Badges are placed in a 1,500-degree furnace following the application of a first coat of enamel. Photo by Steven Georges/Behind the Badge OC
Steve Visk says what he loves most about his job is hearing from satisfied customers.
“I love when they call me and tell me how nice the badges look,” he says.
Behind the Badge recently visited V&V Manufacturing, which employs eight people, most of them longtime employees who have honed their craft over the years.
The process of making a badge starts with the sheet material: 14-gauge solid nickel and brass, purchased from AJ Oster in Yorba Linda. Most badge makers, according to Steve Visk, use plated metal, which is far less durable.
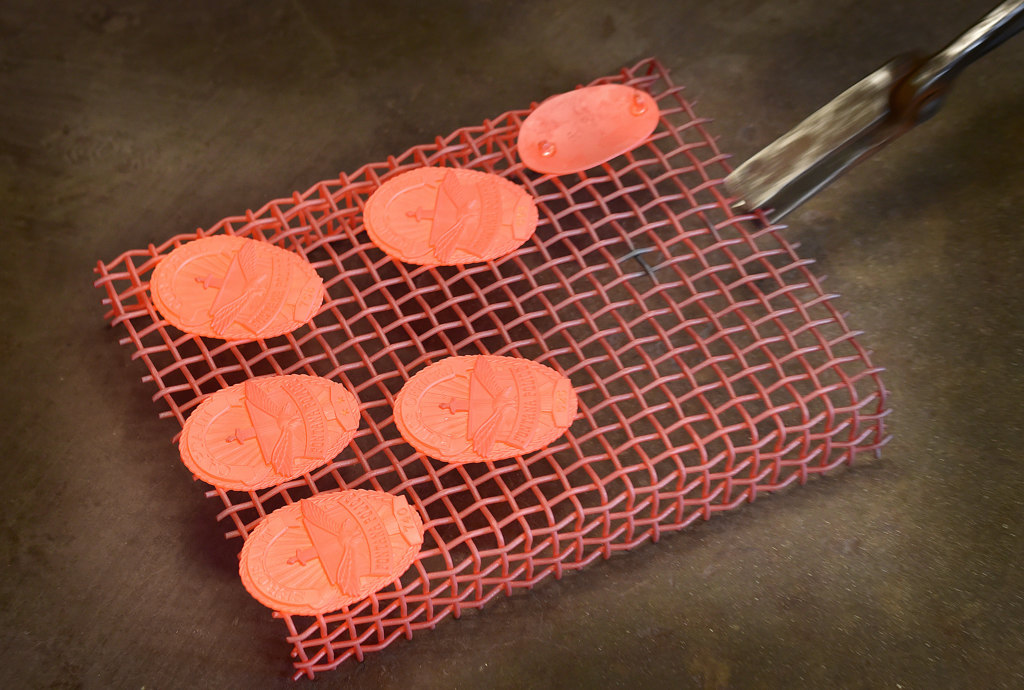
Police badges come out of the furnace red hot before they cool down.
Photo by Steven Georges/Behind the Badge OC
And, as opposed to epoxy paint used by most badge makers, V&V uses hard-fired cloisonné enamel. It never fades, and V&V puts a lifelong guarantee behind that claim.
Here are the steps V&V goes through when making a badge:
Making blanks — Cutters are set up to specific shapes to make the actual blanks for each part.
Stamping — A 600-pound, gravity-drop hammer stamps the blanks into the dies.
Trimming — Excess material from the stamping process is cut off.
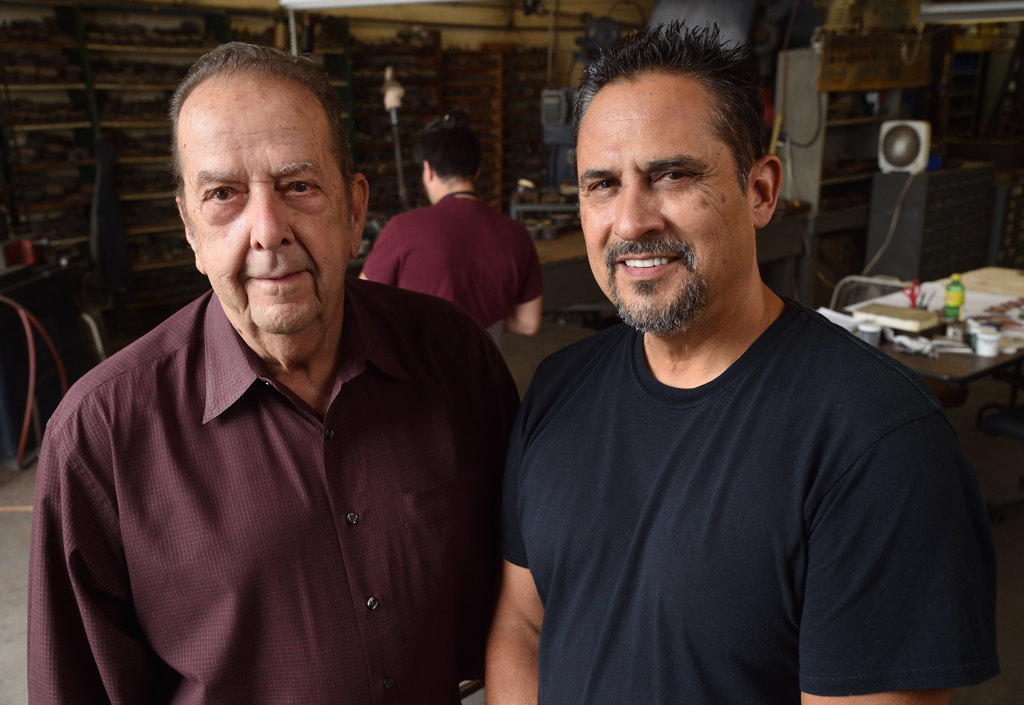
Everett Visk and his son, Steve, run V&V Manufacturing in City of Industry. Photo by Steven Georges/Behind the Badge OC
Silver soldering – This is the process in which parts are soldered to the base piece. V&V uses a solder that melts at 1,500 degrees in two minutes to create a durable bond.
Form — After the badges cool down from the soldering process, they are put in a “kick press” machine that forms them to the specific badge. There are four types: a cylinder form, eagle top form, LAPD form, and star form.
Soldering the joints and catches – V&V uses the same silver solder that is used to weld the parts to the base in process No. 4. The badges then go back into the furnace for two minutes so a durable bond can be created.
Cleaning the fire scale – V&V uses a very diluted sulfuric acid that cleans off the fire scale from the raw metal material.
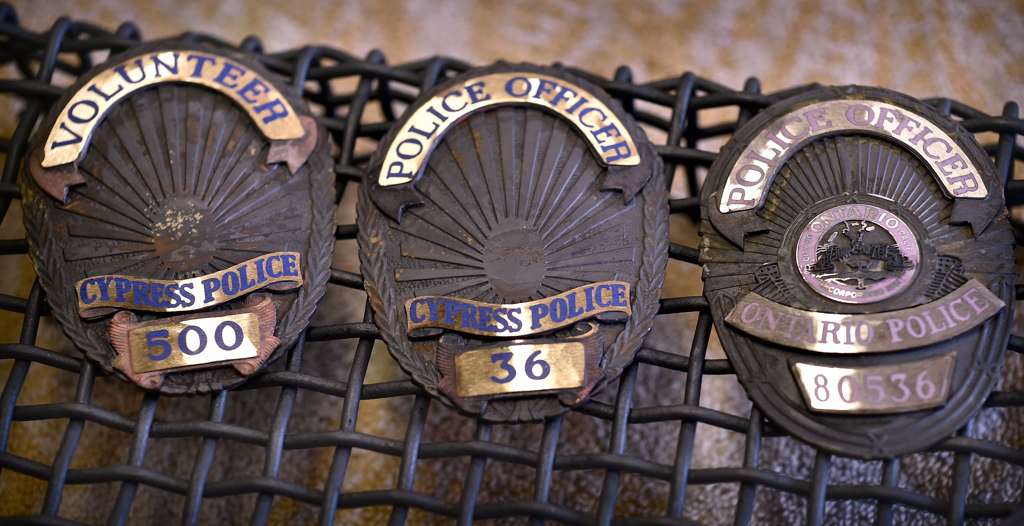
Badges ready for a final session in the furnace after they’ve been ground. Photo by Steven Georges/Behind the Badge OC
Enameling – V&V uses a hard-fired enamel that runs at 1,500 degrees. This process will take two coats of enamel to ensure every area of the letters is full, with no low areas or imperfections.
Grinding — A wet grinding belt is used to grind the enamel after the grinding process. The badges must go into the kiln once more to get the glass look from the enamel. They then go back into the sulfuric acid solution to get the fire scale off from the oven.
Pumice — This process removes the fine-grinding marks from the belt used to grind the enamel.
Brushing — V&V uses a small brush to polish between the cracks and crevices that the larger polish wheel will not reach in the next process.
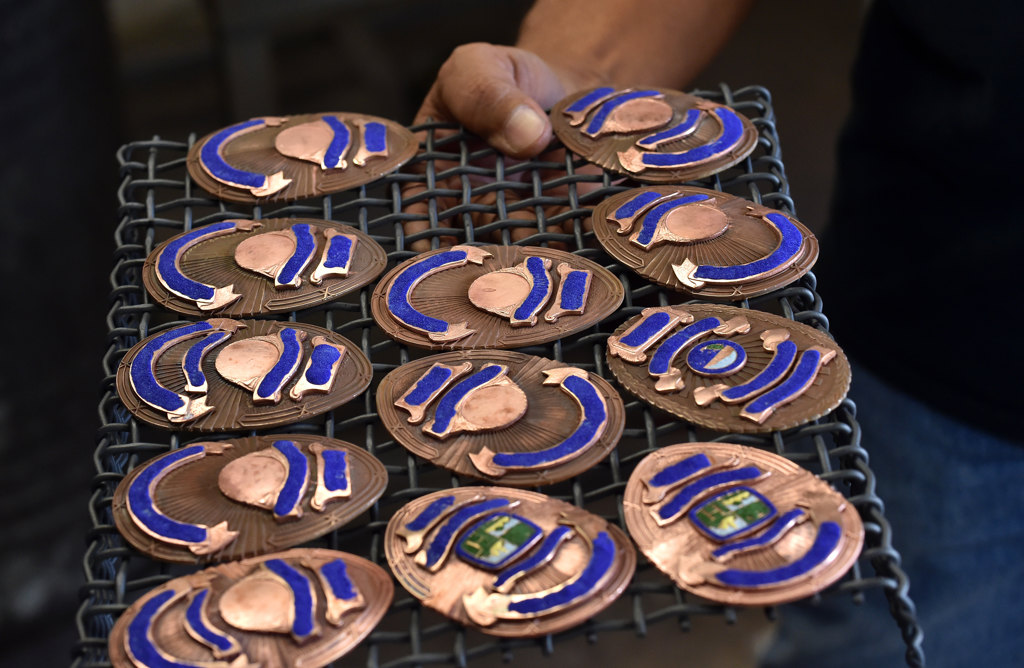
Badges are ready to be placed in a 1,500-degree furnace following the application of a first coat of enamel. Photo by Steven Georges/Behind the Badge OC
Final polish — The badge is polished with a large buffing wheel to remove all scratches and imperfections.
Rouge — This process gives the badge a highly polished mirror effect. After this step, the badges are ready for the final stage.
Bake lacquer — The badges are sprayed with a clear-coat lacquer that is baked in an oven at 250 degrees for 15 minutes. After the badges cool down, they’re inspected by at least two people and then shipped.
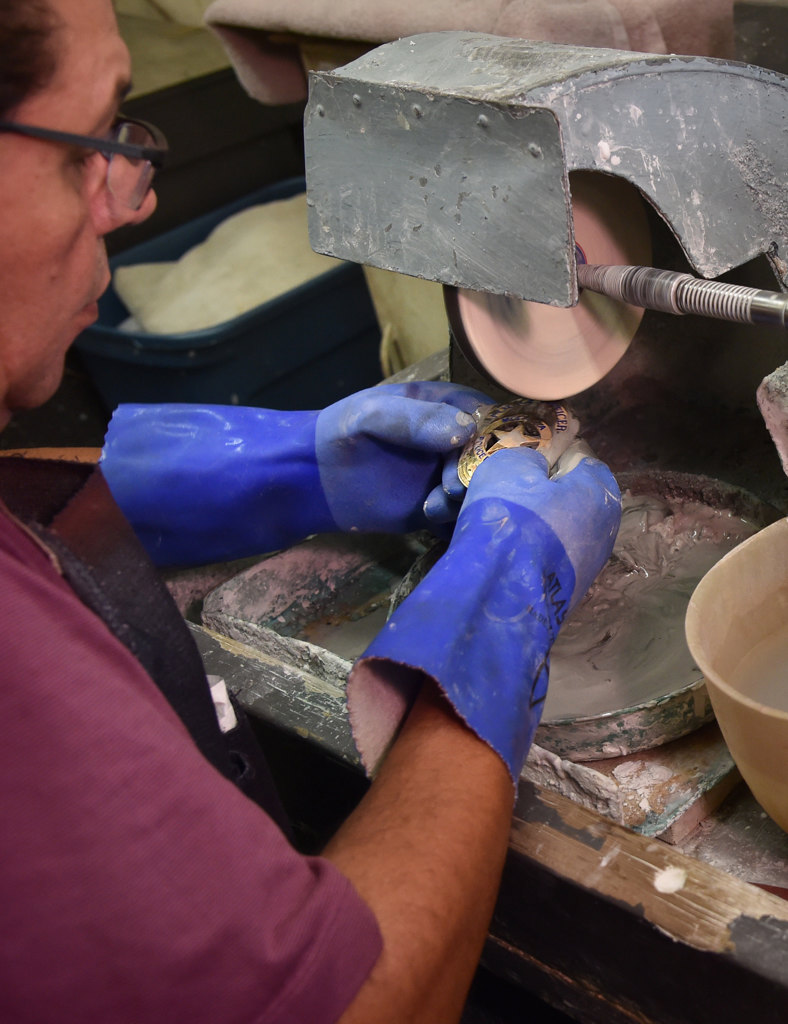
Alejandro Martinez uses pumice to get rid of marks left by the grinding belt.
Photo by Steven Georges/Behind the Badge OC
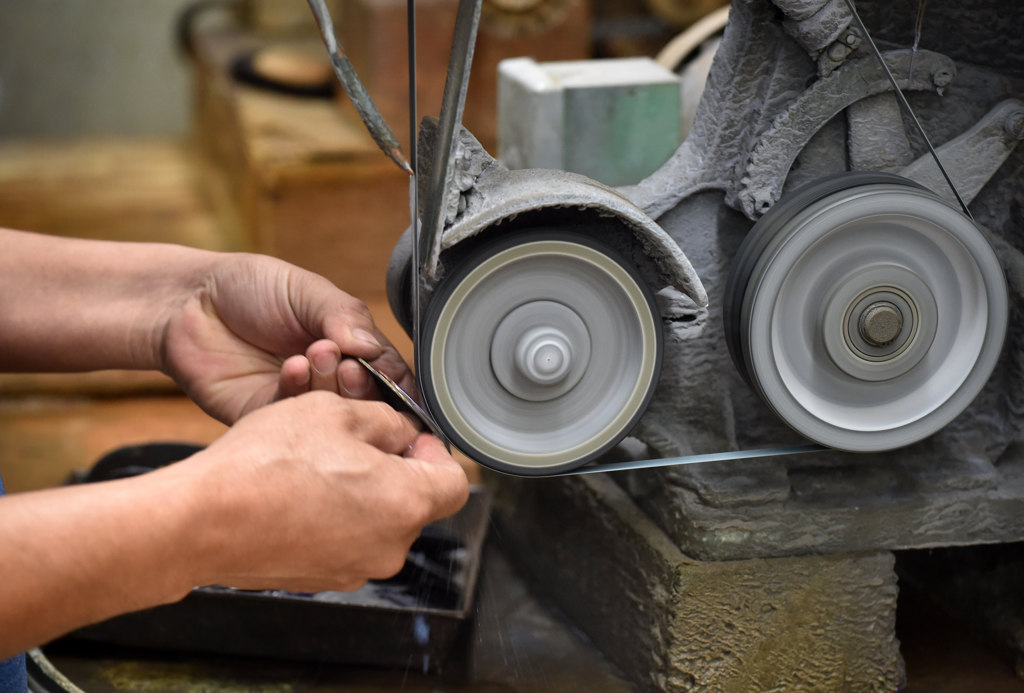
A worker at V&V Manufacturing grinds the enamel on a badge. Photo by Steven Georges/Behind the Badge OC
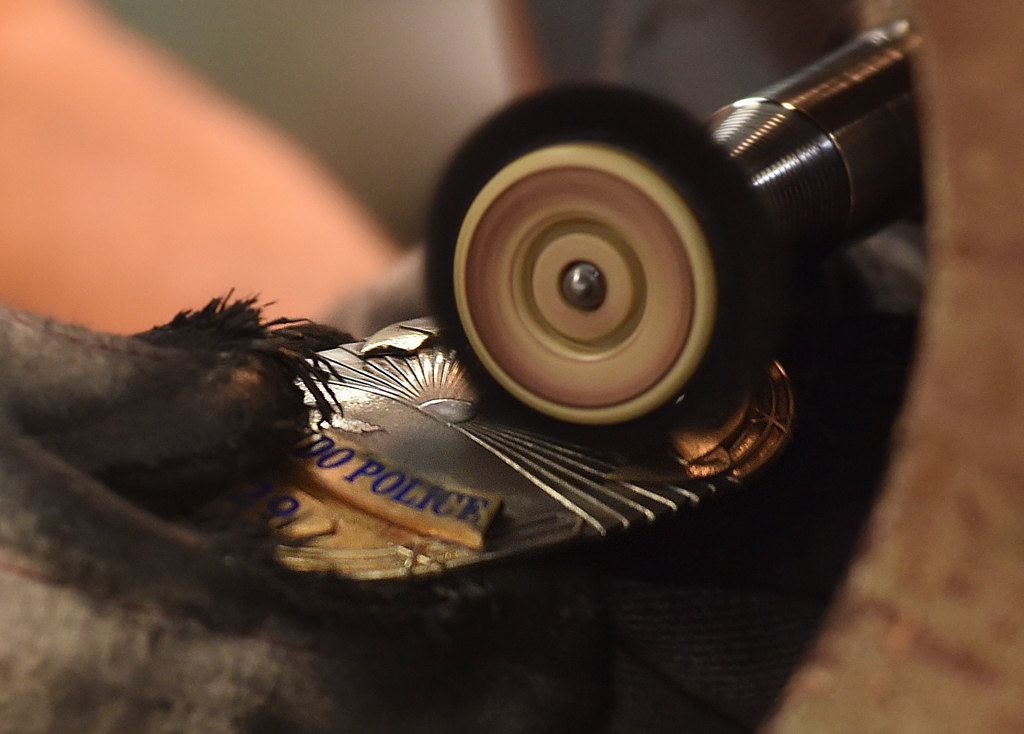
A worker uses a brush to polish hard-to-reach places on a badge. Photo by Steven Georges/Behind the Badge OC
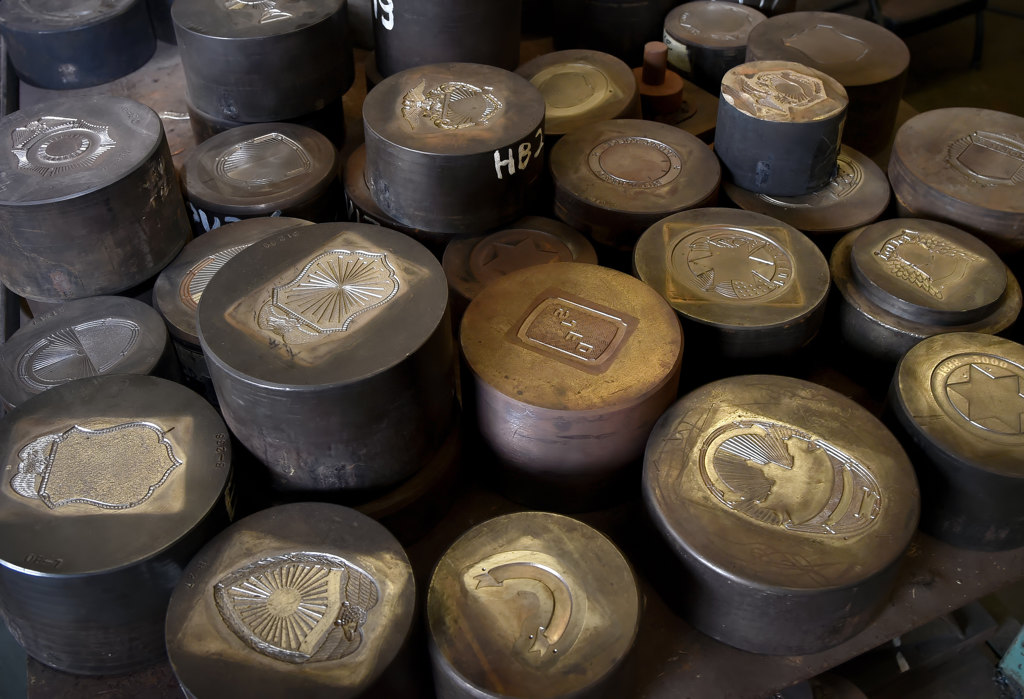
Some of the steel dies used to make badges at V&V Manufacturing.
Photo by Steven Georges/Behind the Badge OC